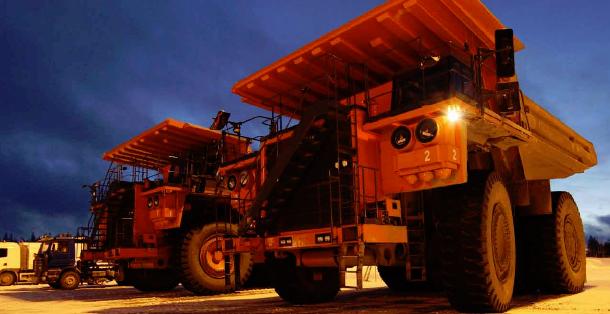
Chief executive officer Harri Natunen explains how the company is using bioheapleaching technology to get the most from its low grade nickel deposits.
Though it is perhaps not the first country that one associates with the industry, Finland’s mining history in fact dates back to 1540. Today the raw material base for its metal industry is made up from the exploitation of nickel, copper, cobalt, zinc and lead ores, as well as chromium, vanadium and iron deposits.
Located in Sotkamo, in the east of the country, Talvivaara boasts two metasedimentary hosted, low grade nickel sulphide ore bodies, Kuusilampi and Kolmisoppi. Originally discovered by the Geological Survey of Finland in 1977, the deposit was at first deemed to be too poor for existing technology. It was determined at this early stage that the only process that would be capable of concentrating the nickel enough would be bioheapleaching, a technology which, at that point, remained untested in such a scenario.
Obtained by Outokumpu Corporation, the mining rights were eventually sold to one of its former employees, Pekka Perä. It was Perä’s purchase of the rights that gave birth to the Talvivaara Mining Company in 2004.
Today an internationally significant base metals producer, with its primary focus on nickel and zinc, the company’s Kuusilampi and Kolmisoppi deposits are now recognised as comprising one of the largest known sulphide nickel resources in Europe. Their combined contents of 1.1 billion tonnes of ore, in measured and indicated categories, are thought to be sufficient to support extensive production levels for several decades to come.
Talvivaara supplies metal intermediaries to companies with metal refining operations. Arguably its most important contract to date is the ten year off-take agreement it has entered into with Norilsk Nickel Harjavalta. This agreement involves the delivery of the entire output of the mine’s nickel and cobalt production at market prices. A similar long-term partnership was established in January 2010, with the company entering into a zinc concentrate streaming agreement with Nyrstar NV. The terms of this contract involve the delivery of all of Talvivaara’s zinc concentrate to Nyrstar up to 1,250,000 metric tonnes.
“What makes the work we carry out unique,” explains chief executive officer, Harri Natunen, “is the fact that we apply bioheapleaching technology to extract nickel from the ore.” Commonly used in copper processing, particularly in Central and South America, bioleaching is a process in which metals are leached from ore as a result of a bacterial action. Triggered spontaneously by micro-organisms in the presence of air and water, commercially applied bioleaching technologies replicate the same natural phenomenon, but accelerate the process in order to speed up metal recovery.
“What we do is,” Natunen continues, “we mine the ore, crush it down in four stages to a size of minus 15 millimetres and then utilise a process of agglomeration using a pregnant leach solution.” After the agglomeration process the ore is conveyed and stacked eight metres high on the primary heap pad to undergo one and a half years of bioheapleaching. The heap pad is equipped with piping and laid on the bottom of the pad, through which low-pressure fans supply air to the stacked ore. From the top, the heap is irrigated with leach solution, which is recycled through the heap until its metal content is sufficient for metals recovery.
Following its time on the primary pad the leached ore is then reclaimed, conveyed and re-stacked onto a secondary heap pad, where it is leached further to recover metals from those parts of the primary heaps where the leach solution couldn’t previously penetrate. After secondary leaching, the barren ore remains permanently on the secondary heaps.
“The total leaching process,” Natunen says, “takes approximately five years, at which point the pregnant solution is collected, with the majority being pumped to a metals production plant where it is infused with hydrogen sulphate. These materials are precipitated as sulphites and then, through a combination of dewatering, thickening and filtration the final product is processed ready for delivery.”
Bioheapleaching was chosen as the preferred technology for the Talvivaara mining project based upon its favourable capital and operational cost profile. A low cost process requiring only air, sulphuric acid, water and microbes to work, bioheapleaching has lower capex and opex than traditional grinding and flotation processes. It is also widely recognised as a cleaner and more environmentally friendly process.
The concept of responsible mining exists throughout Talvivaara’s business operations and incorporates three dimensions of corporate social responsibility, these being economic, environmental and social aspects. Across its operations the company seeks to meet the challenges associated with achieving sustainable development.
The primary objective of Talvivaara’s environmental management is to ensure the sustainable and economical use of natural resources, while at the same time minimising any adverse effects on the environment that could be caused by its mining operations. From a social perspective, the company is equally as committed to the development of its employees, encouraging them to acquire and develop the necessary professional skills.
“In all that we do,” Natunen states, “our aim is to be a pioneer within the mining industry. As a young company we have had the opportunity to develop responsible best practices from the offset, while introducing environmentally efficient technology at every possible turn. As a result of a combination of an eco-efficient metals recovery process, the very best new technology, an advanced operating environment, and a high level of expertise, we are in a prime position to be able to grow into our desired role of being a leading player in responsible mining.”
Today, the company finds itself on the cusp of making its first test delivery of copper concentrate, marking another milestone in its short history. In addition to this, Talvivaara has recently entered into a co-operation agreement with Cameco, one of the world’s largest publically traded uranium companies. This partnership will allow Talvivaara to make use of the uranium by-product which is created during the bioheapleaching process. Furthermore, the company has entered into the construction phase of its building of a uranium recovery plant. This project is expected to be completed during the first six months of 2013 and will create an additional revenue stream for the business.
“When Pekka Perä first set about developing this operation,” Natunen says, “he worked especially hard to bring together a group of individuals that boast experience and expertise in different areas of mining, as well as those that specialise in the use of bioheapleaching. In doing so he has created a company that, while still in its ramp-up phase, has incredible potential and the ability to increase its production levels, and achieve the cash-cost position it is targeting. What Perä has managed to do in such a short space of time is already a well-recognised achievement here in Finland, and I’m sure it will only continue to garner the attention of the mining world as a whole as time passes.”
Written by Will Daynes, research by Jeff Abbott
DOWNLOAD
Talvivaara-EMEA-Dec12-Bro-s.pdf